Na czym polega Industria 4.0, czyli czwarta rewolucja przemysłowa?
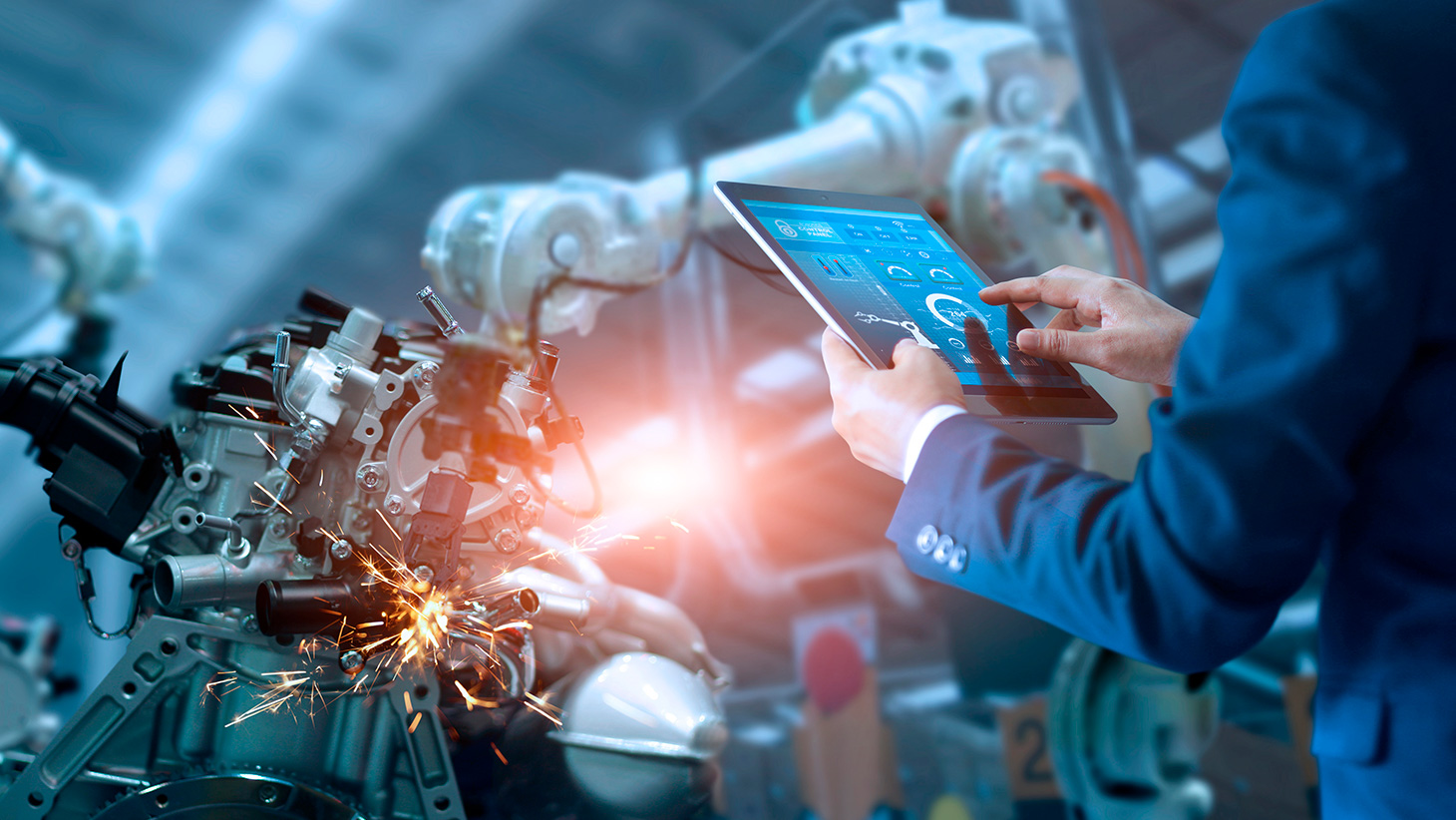
Industria 4.0, znana również jako czwarta rewolucja przemysłowa, jest terminem szeroko stosowanym do opisu nowoczesnych technologii i podejść, które przekształcają tradycyjne procesy przemysłowe i systemy produkcyjne. Termin ten został po raz pierwszy użyty na Hannover Messe w 2011 roku w Niemczech i od tego czasu stał się synonimem integracji nowych technologii cyfrowych w przemyśle.
Głównym celem Industrii 4.0 jest zwiększenie efektywności, elastyczności oraz indywidualizacji produkcji, a także poprawa jakości i bezpieczeństwa.
Jej technologie obejmują m.in. Internet Rzeczy (IoT) – umożliwia urządzeniom komunikację i wymianę danych między sobą przez internet; Sztuczna inteligencja (AI) i uczenie maszynowe – pozwalają maszynom na uczenie się z danych i automatyzację złożonych zadań; Robotyka i automatyzacja – ulepszają efektywność i precyzję procesów produkcyjnych; Big Data i analiza danych – umożliwiają analizę ogromnych ilości danych w celu uzyskania lepszego zrozumienia i optymalizacji procesów; Druk 3D: Technologia ta pozwala na szybką i elastyczną produkcję elementów według indywidualnych wymagań, bez konieczności uruchamiania masowej produkcji.
Te technologie przyczyniają się do zwiększenia efektywności, zmniejszenia kosztów, i oferują nowe możliwości dla biznesów, ale też rodzą wyzwania, takie jak bezpieczeństwo danych i konieczność przekwalifikowania pracowników. Poprzednie rewolucje przemysłowe miały również głęboki wpływ na sposób produkcji i organizację pracy. Przypomnijmy je sobie.
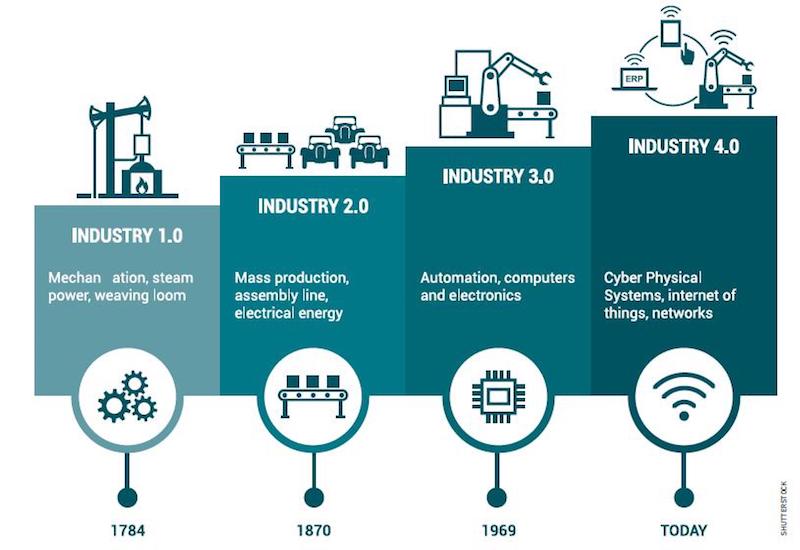
Pierwsza rewolucja przemysłowa (ok. 1760-1840)
Rozpoczęła się od wprowadzenia maszyn parowych i mechanizacji pracy, szczególnie w branży tekstylnej i górnictwie.
Druga rewolucja przemysłowa (ok. 1870-1914)
Charakteryzowała się rozwojem produkcji seryjnej, elektryfikacją i rozbudową sieci kolejowej. W tym czasie pojawiły się takie wynalazki jak silnik spalinowy i telefon.
Trzecia rewolucja przemysłowa (ok. 1960-1990)
Znana również jako „rewolucja cyfrowa”, przyniosła automatyzację produkcji za pomocą elektroniki i technologii informatycznych, w tym komputerów osobistych i robotów przemysłowych.
Industria 4.0 nie jest tylko przemianą technologiczną, ale przede wszystkim strategicznym i operacyjnym przesunięciem w sposobie, w jaki firmy prowadzą działalność produkcyjną.
To kompleksowy ruch, który zaznacza początek nowej ery w przemyśle, z ogromnym potencjałem do transformacji globalnych łańcuchów dostaw i rynków pracy. Niesie też ze sobą szereg zagrożeń i wyzwań, z których wymienić należy przede wszystkim:
Bezpieczeństwo cybernetyczne
W miarę jak więcej urządzeń zostaje podłączonych do sieci w ramach Internetu Rzeczy (IoT), wzrasta ryzyko ataków cybernetycznych. Przemysłowe systemy sterowania oraz dane produkcyjne mogą stać się celami dla hakerów, co może prowadzić do kradzieży danych, zakłóceń w produkcji, a nawet uszkodzenia sprzętu.
Prywatność danych
Wiele systemów Industrii 4.0 gromadzi i przetwarza ogromne ilości danych, co rodzi pytania o prywatność i etykę w zarządzaniu tymi informacjami. Zagrożenie dla prywatności nie dotyczy tylko danych osobowych pracowników, ale również wrażliwych informacji biznesowych i technologicznych.
Zawodność technologii
Zależność od skomplikowanych systemów automatycznych i algorytmów AI może prowadzić do nieprzewidzianych awarii. Błędy w oprogramowaniu, nieoczekiwane interakcje między systemami czy awarie sprzętu mogą prowadzić do poważnych przerw w produkcji.
Zmiany na rynku pracy
Automatyzacja i robotyzacja, kluczowe elementy Industrii 4.0, mogą prowadzić do zmniejszenia liczby dostępnych miejsc pracy dla nisko kwalifikowanych pracowników, co może przyczynić się do wzrostu bezrobocia i nierówności społecznych.
Wprowadzenie zaawansowanych technologii wymaga od pracowników nowych umiejętności i adaptacji.
Firmy muszą inwestować w szkolenia, aby ich pracownicy mogli efektywnie pracować z nowymi systemami, co wiąże się z dodatkowymi kosztami i wyzwaniami w zarządzaniu zasobami ludzkimi.
Zależność od dostawców technologii
Wysoki stopień złożoności technologicznej może prowadzić do zależności od niewielkiej liczby dostawców specjalistycznego sprzętu i oprogramowania. Taka zależność może ograniczać elastyczność operacyjną i negocjacyjną przedsiębiorstw.
Kompleksowość zarządzania
Integracja systemów, zarządzanie danymi w czasie rzeczywistym i zapewnienie ciągłości działania wymagają skomplikowanych strategii zarządzania i ciągłego monitorowania. Wymaga to od firm nie tylko inwestycji finansowych, ale również rozbudowy kompetencji zarządczych.
Normy prawne i regulacje
Rozwój technologii przemysłowych często wyprzedza rozwój odpowiednich ram prawnych i norm regulacyjnych. Firmy muszą na bieżąco śledzić zmiany w prawodawstwie, co może być wyzwaniem, szczególnie w kontekście globalnym.